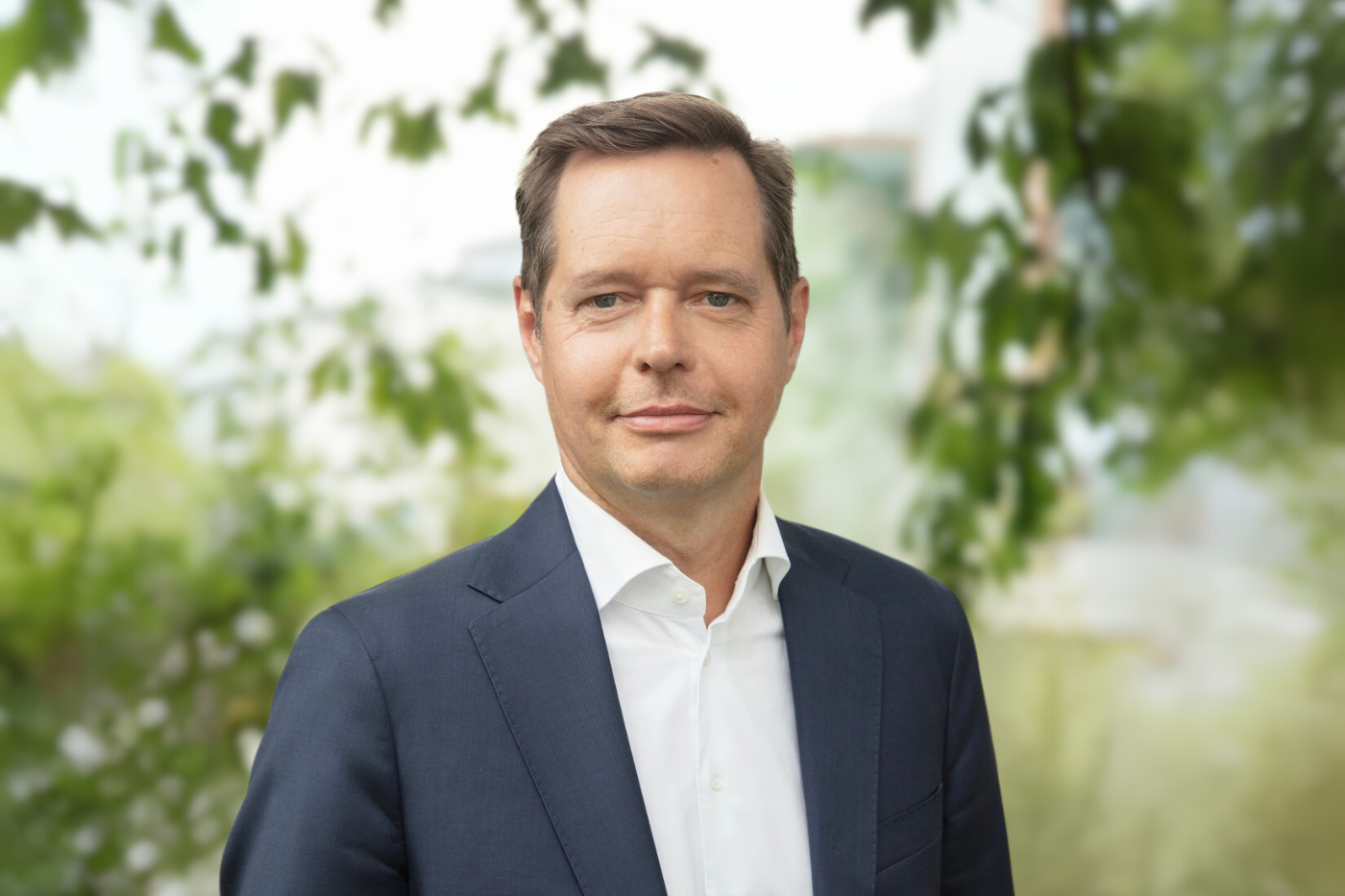
AkzoNobel announces Fredrik Westin as Chief Financial Officer from January 1, 2026
Jul 03, 2025
Subscribe to news alerts by e-mail so you don’t miss a thing! Whether it’s about our pioneering innovations, new product launches, sustainable initiatives, exciting partnerships, business announcements or our latest financial results – we can deliver all the news straight to you.
Looking for AkzoNobel-related media such as our logo, product photos, building and landmarks we’ve coated or footage from one of our sites? A wide selection of images and other digital assets from this library are available for restricted use.
If you're a journalist and looking for more information about media releases and events, please contact our media relations team. They’ll be able to provide direct and prompt assistance.